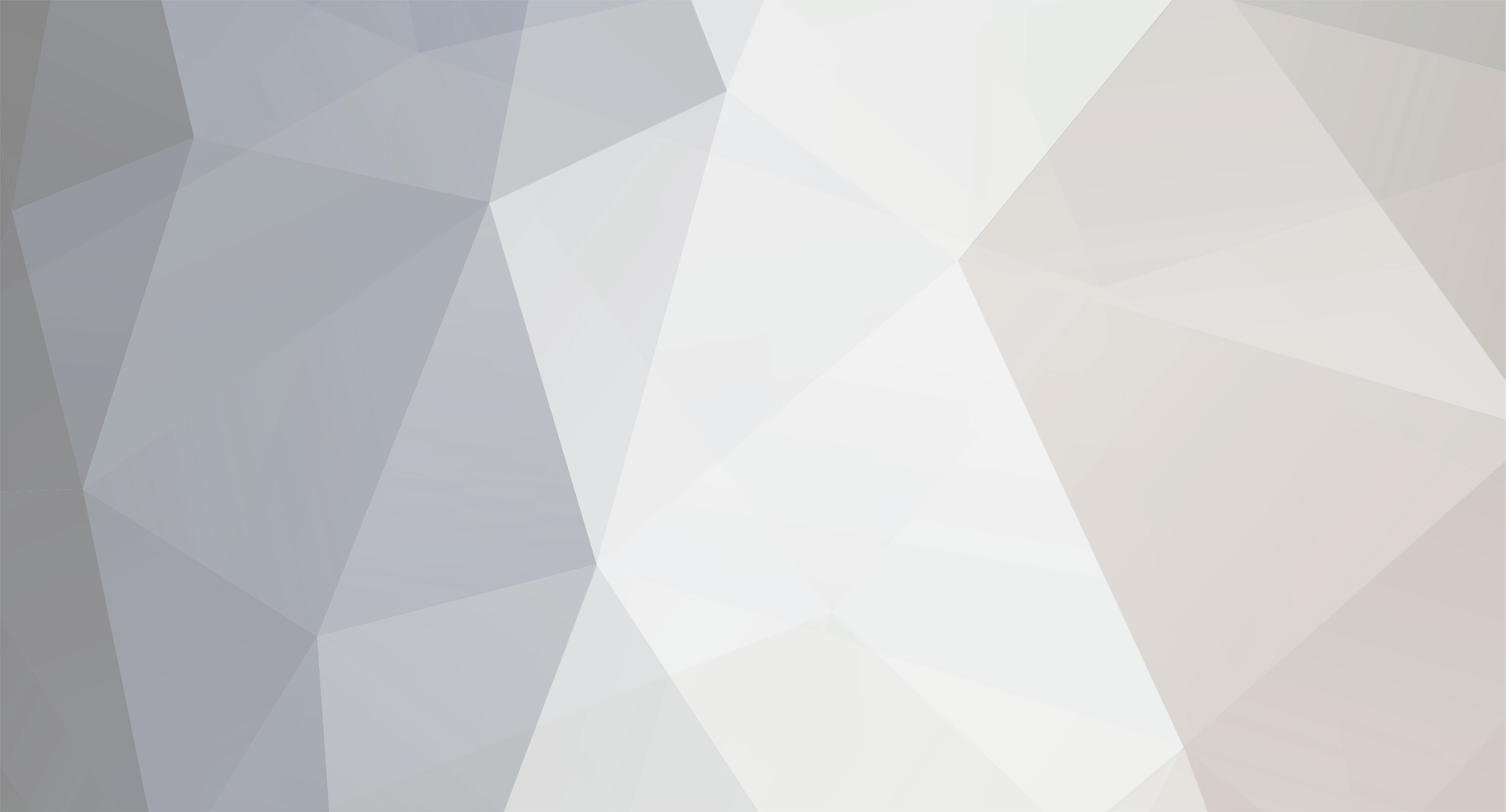
Boz
-
Posts
5 -
Joined
-
Last visited
Content Type
Profiles
Forums
Events
Media Demo
Store
Collections
Videos
Posts posted by Boz
-
-
This is pretty awesome seeing the amp go from thought to production. I used to work in the engineering and testing department for a company that produced telephony equipment so I have done my fair share of testing (and also repairing what the engineers break lol.) I also worked in vending/amusement repair so we got to play with a ton of high current MOSFETS/Transistors etc.
Have you thought about using: http://www.bergquistcompany.com/thermal_materials/hi_flow/hi-flow-300P.htm, It is phase change like you were using before but is made for high current applications. I bet the ceramic is a nice material but I have my doubts that on a microscopic level that it is maintaining complete contact with a porous material such as Al..
You need to get Magic Juan some magic tools!
Looks like he will need a solder fume extractor (solder fumes are not good to keep breathing in and need to be evacuated for employee health)
Get that man a hot air rework station and solder paste for SMD work! You will find his solder joints improve exponentially
He needs a tip cleaner/tip tinner too for the soldering iron and a new tip!
A raise lol.
Awesome work.
How much do one of your amps run for either home or car audio?
Thanks Boz. Yeah we tried several types of the high flow material, 300, 600 and 2000. It is good, but not as good as the ceramic. Yes the ceramic has to be used with a very thin layer of thermal grease for those microscopic imperfections.
Juan has all of those tools on his bench, anytime you see him using a burned up pos Hakko he is on my bench lol.
The home amp isn't for sale, this model of the car amp has a MSRP of $4199. This is introductory and could change. There are 3 more models to follow with the same design.
The home amp looks pretty awesome, the car amp is amazing too but I'm sure my car would lose a lot of acceleration and the amp would hate autocrossing lol.
I see you use Tenma stuff, been using it for years and the company that makes most of the Tenma equipment white labels it for other manufacturers. They are very competitive for the price. Xytronics also makes decent mid grade equipment.
Have you thought about a basic FLIR based camera system while stress testing to see all of the hot spots? You can rent/lease them from some suppliers which cuts down on the cost. For about $60 you can build a microcontroller based temperate station with something like a Raspberry pi and monitor about 10 temp ic's greased onto the heat sinks and transistors. Might give you a better idea as to the best way to cool 1,000,000 watts of power haha.
Do you think utilizing a quad array of high speed micro fans facing longitudially and all blowing into the same direction so you have an intake and exhaust would provide for better cooling across the MOSFETS? Some of the issue with high power MOSFETS is heat saturation so once you hit saturation it is that much harder to keep the temperature rise down.
-
This is pretty awesome seeing the amp go from thought to production. I used to work in the engineering and testing department for a company that produced telephony equipment so I have done my fair share of testing (and also repairing what the engineers break lol.) I also worked in vending/amusement repair so we got to play with a ton of high current MOSFETS/Transistors etc.
Have you thought about using: http://www.bergquistcompany.com/thermal_materials/hi_flow/hi-flow-300P.htm, It is phase change like you were using before but is made for high current applications. I bet the ceramic is a nice material but I have my doubts that on a microscopic level that it is maintaining complete contact with a porous material such as Al..
You need to get Magic Juan some magic tools!
Looks like he will need a solder fume extractor (solder fumes are not good to keep breathing in and need to be evacuated for employee health)
Get that man a hot air rework station and solder paste for SMD work! You will find his solder joints improve exponentially
He needs a tip cleaner/tip tinner too for the soldering iron and a new tip!
A raise lol.
Awesome work.
How much do one of your amps run for either home or car audio?
http://damoreengineering.com/collections/audio-amplifiers/products/dual-mono-power-amplifier
Thanks, yeah I knew that it was more of a question for the original poster.
-
This is pretty awesome seeing the amp go from thought to production. I used to work in the engineering and testing department for a company that produced telephony equipment so I have done my fair share of testing (and also repairing what the engineers break lol.) I also worked in vending/amusement repair so we got to play with a ton of high current MOSFETS/Transistors etc.
Have you thought about using: http://www.bergquistcompany.com/thermal_materials/hi_flow/hi-flow-300P.htm, It is phase change like you were using before but is made for high current applications. I bet the ceramic is a nice material but I have my doubts that on a microscopic level that it is maintaining complete contact with a porous material such as Al..
You need to get Magic Juan some magic tools!
Looks like he will need a solder fume extractor (solder fumes are not good to keep breathing in and need to be evacuated for employee health)
Get that man a hot air rework station and solder paste for SMD work! You will find his solder joints improve exponentially
He needs a tip cleaner/tip tinner too for the soldering iron and a new tip!
A raise lol.
Awesome work.
How much do one of your amps run for either home or car audio?
How to design an amplifier
in D'Amore Engineering - High Quality Car Audio Installation Tools & Accessories
Posted
True most amps build the mass into the finned top cover and have the solid heat sinks bars attached to the top cover, nothing as robust as a brick of solid metal. I'd like to see those heat chimneys in action, maybe throw a little smoke into the fans while the amp is stressing? I bet it would make for a good promo video. These amps are way overkill for my puny JL Audio twin 10W3v3's and Boston Pro 6.5's.
Have you considered doing small form factor 4 or 5 channel designs? I'm sure the complexity goes up exponentially in dealing with higher frequencies.